What is glass polishing?
Glass polishing is the removal of scratch and mineral damage from glass surfaces using a polishing machine and a series of abrasive pads and polishing actions.
Using glass polishing systems, a skilled glass polisher can remove almost any form of scratch, mineral or spatter damage from any glass surface.
Glass polishing, as with any young industry, has taken a while to become accepted by the business sector, but over the last few years more and more construction companies, high street retailers, homeowners and public transport companies have come to realise the benefits that glass polishing offers and now regularly use services such as ours to protect the image of their businesses.
The history of glass polishing 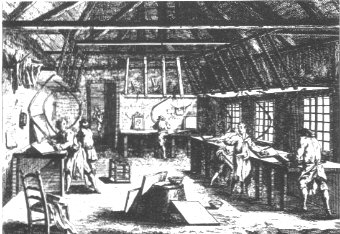
The process of glass polishing was first developed in France back in 1688 as a finishing stage in the production of plate glass. At this time, the optical quality of glass left much to be desired.
With the plate glass placed on large round tables, rotating iron discs and increasingly fine abrasive sands were used to remove scratches and blemishes from the glass surface before being polished with felt pads to complete the process. By 1773, the French glass polishing system was adopted by the English at Ravenshead and by 1800 a steam engine was used to power the grinding and polishing tables for plate and cast glass polishing.
As glass manufacturing developed and the quality of production improved, the need for glass polishing services in its traditional form, all but disappeared. it wasn’t until the late 80’s that glass polishing started to reappear, mainly within the auto windscreen market. Hand held power tools used felt pads and abrasive compounds to remove light scratches and stains from auto glass.
How it works
Since then, there have been numerous advances in repairing scratched glass, but the basic theory behind the techniques remain the same as they were back in 1688. A powered rotary disc using abrasives to remove glass to the depth of the scratch and to blend and polish the area worked back into the surrounding glass.
Starting with a 120 or 180 grit sanding pad and a mechanical polishing machine the scratched area is ground down to level of the scratch thus removing it. Then working through finer grades of sanding pad to finish at either 500 or 1000 grade pad depending on a number of factors and the decision of the technician at the time. At each stage the repaired area is increased by moving further out from the initial damaged area to ‘blend’ of ‘feather in’ the repair to the surrounding glass. This ensures that no distortion or dishing remains.
Once the sanding is complete there is then a polishing stage using a felt pad on the polisher and a polishing compound. Using water from a spray bottle to cool the glass the repaired area is then polished. This is then repeated working the repaired area into any surrounding or unworked glass.
The area is then cleaned down and tidied up and there will be no evidence that any scratches existed in the glass.
Due to the nature of how the system works any damage within 30mm of the glass may not be able to be removed. This is due to having no surrounding glass on one edge to blend into causing distortion in the glass. Also when polishing the felt pad needs to overlap the worked area to enable a clear finish. When working close to the edge this can’t be done so a hazy or misty finish will be left around the frame.